Parcel & DC Material Handling
Solutions for Parcel & Distribution Centers
During Globe’s extensive on-site consultation process over the years at various parcel and distribution facilities, we’ve benefited our clients the most by using their maintenance experiences to re-engineer problematic components and assemblies. Using our composite polymers along with better component designs we improve performance, and reduce their overall maintenance costs.
We have helped many clients by reverse engineering parts to systems that are no longer supported by the original equipment manufacturer, allowing them to extend the life of their equipment rather than make a substantial capital investment in new equipment.
The results generally include reduced weight, energy, downtime, maintenance costs, and wear, with extreme impact resistance, and a significant reduction in noise levels.
How can Globe help your company with:
- Energy Savings through Reduced Product Weight
- Significant Noise & Vibration Dampening
- Durable, Safe Tools for Improved Operational Efficiencies
- Reduced Downtime
- Increase Throughput
- Abrasion & Wear Resistant Parts
- Extreme Impact Resistant Parts
Sample Material Handling Products
The team at Globe Composite can design and produce a wide variety of equipment for distribution facilities, from all or mostly composite-based materials. We can custom blend these materials to exactly meet your product’s specific requirements, so you can rest assured that your part will perform as expected- each and every time.
Custom Conveyor Rollers
We design and manufacture custom conveyor rollers, to meet the needs of your business. Including Tapered Conveyor Rollers, Non-Metallic Conveyor Rollers, and Covered Conveyor Rollers.
> Learn More
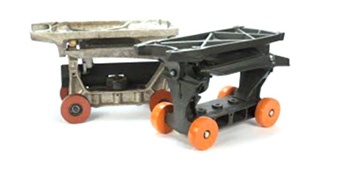
Tilt Tray Sorters
Extend the life of your sortation equipment by replacing metal, rubber, or plastic parts with Brandonite®, including carriages, tracks, chains, wheels, and tip-up actuation devices. > Learn More
Jam Break Poles
Unjam baggage using our long-lasting composite-based Jam Break Poles. Three tool types for all conveyor uses. Safely remove baggage from X-Ray Scanners and Explosive Detection Systems as well. > Learn More
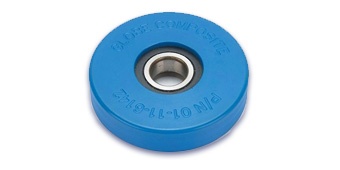
Crisplant Replacement Wheels
Urethane Replacement Wheels for Crisplant LS-4000E or Crisplant LS-3000DT Sorters. We design a wide range of replacement parts or urethane wheels for Crisplant sorters. > Learn More
Sandvik Diverter Replacement
Drop-in Replacement for the Sandvik Diverter Paddle. We re-engineered the attachment arm with a double gusset, that goes all the way from the point of attachment to the crank arm. (No More Weld Repairs!)
> Learn More
Shaftkeeper II®
Extend the Life of Your Conveyor Systems. Shaftkeeper II ® is our easy-to-install, patented part which will extend the life of your conveyor system, giving you even more years of trouble-free use.
> Learn More
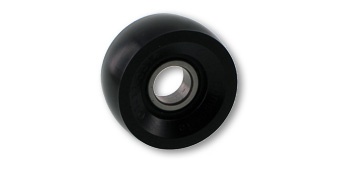
Siemens Loader Wheels
Globe produces hard to find Siemens loader wheels. These urethane guide wheels are for use on an Siemens extendable conveyor systems.
Wheels & Rollers
Replacement wheels for even the most demanding applications, including DCV sync wheels, pallet jack rollers, or sorter wheels. Our unique process ensures that the wheels are balanced for long-lasting, vibration-free use.
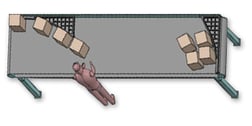
Guides & Diverters
Designed to mount to conveyor side rails for repositioning parcels, baggage, totes or any other items that might be conveyed on belt or roller systems.
> Learn More
About Us
Globe is changing the world with composite solutions, and offers a full spectrum of services ranging from the initial material formulation, to the scalable production of your finished component.
Contact Us
For more information, please fill in our online enquiry form or contact our sales offices directly at +1 781-681-6802. From concept to production, we've had over 130 years of experience providing extraordinary solutions to complex problems.