In any parcel or distribution facility, there are several pieces of equipment that are critical to operations. Tilt-tray sorters, diverter arms, actuators, and conveyance components all keep business operations running smoothly. Packing and shipping tools, such as palletizers, trailers, and trucks, play an integral role in the efficient movement of parcels. Unfortunately, each of these critical tools can experience issues that disrupt performance.
Downtime can be costly and disrupt the flow of your whole enterprise. There is nothing more frustrating than watching an essential piece of equipment sit idle. Are these frustrations just a part of the job, or is there something you can do to minimize unscheduled downtime?
Identifying the Root Cause of Downtime
Any unscheduled downtime can have a snowball effect. When facility equipment breaks or otherwise malfunctions on a regular basis, the business loses money, time, and may even run into customer service issues. Excessive and repeated downtime often plagues the materials handling industry because of continued use of metal-to-metal components. Enhancements and adjustments don’t provide a long-term solution, they simply buy maintenance managers a little more time – at a hefty price.
Even if a maintenance manager is successful in determining the root of the problem and develops an effective solution, they may need to wait an extended period of time before they can get a working prototype into their system to test. Managers are tasked with determining the best solution given their constraints – such as time, money, and available resources. Distributors cannot take machines offline for extended periods of time to replace them, nor can they shoulder the large financial burden of a brand-new system.
How to Reduce Downtime Using a Strategic Component Replacement
Over our years of onsite consulting at various parcel and distribution facilities, we’ve found that one of our clients’ biggest problems was finding a solution for metal-on-metal components leading to repeated unscheduled downtime. As a solution, we've provided our clients with an innovative solution by replacing currently used materials on existing system components.
By replacing metal-to-metal components with polymer composites, material handling facilities have improved the infrastructure that had previously caused systemic failures throughout the enterprise.
Composites offer a superior alternative to traditional metals, plastics, or rubbers. Tough as steel or softer than rubber, our material formulation experts can custom blend a material that will perfectly meet your application's unique requirements. Composites also provide a proactive approach to future price increases, especially due to steadily rising price of steel since 2009. Additionally, composites consume roughly half as many natural resources and energy during production than aluminum or steel - making it the sustainable choice.
As a full service design and manufacturing company, we can review a system or component to identify the problem, then engineer and design a solution in-house using composite materials. Some firms are only design houses, who will leave the prototyping to another firm. With a design and manufacturing partner, companies can rapidly prototype models that allow them to test the function and fitness of the component in real-world scenarios.
Real-World Scenario: All-Composite Diverter Arms
One of our customers was using motor-activated diverter arms to push packages and non-standard objects off high-speed conveyors into delivery chutes - at two of its largest distribution centers. Made of reinforced aluminum and steel, the diverter arms would deform or crack from repetitive stress. Frequent, unscheduled downtime in the facility’s fleet of 5,000 diverter arms was causing issues in business operations and customer service. The customer tried numerous enhancements, with no success.
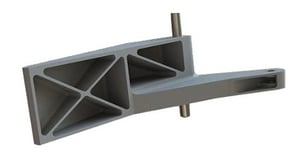
After consulting with the client, we created a one-piece diverter and attachment arm made of lightweight, impact resistant Brandonite® 1000-75D. Our All-Composite Diverter Arm was facility tested for over 2 million cycles without any signs of stress, wear or degradation. This client saved an estimated $1.1 million over the next three years in replacement costs and prevented unscheduled downtime. (Read the full case study here)