As the engineer responsible for ensuring the performance and safety of sealing components, there can be quite a lot of pressure riding on making the proper material selection for a specific application. Before you even begin to think about installing and testing a new gasket, you are tasked with the critical responsibility of selecting a material that is compatible with the surrounding environment, can withstand the operating temperature and pressure, and is flexible enough to achieve a proper seal.
A History of Risky Sealants
Right up until the 1980’s, asbestos-based sheet packing was commonly used to make commercial and industrial gaskets. Asbestos’ resistance to high temperatures, durability, flexibility, and its relatively affordable cost made it ideal for gaskets. As we now know, asbestos leads to an estimated 3,000 cases of malignant mesothelioma annually, with the majority caused by work-related exposure. When the sheet packing material was cut, sawed, sanded, or damaged in any way, microscopic asbestos fibers would be released into the air, creating a very dangerous work environment.Placing Environment Above All Else
With a drastic need for gaskets that were asbestos-free yet provided comparable levels of durability, flexibility, and resistance, a new generation of gaskets were developed by the sealing industry. These gaskets came in a variety of common materials including:- elastomeric materials such as nitrile rubber, butyl rubber, and styrene butadiene
- fibrous materials such as carbon fibre, glass, and cellulose
- metallic materials such as carbon steel, titanium, and aluminum
- other materials such as flexible graphite, mica, and PTFE
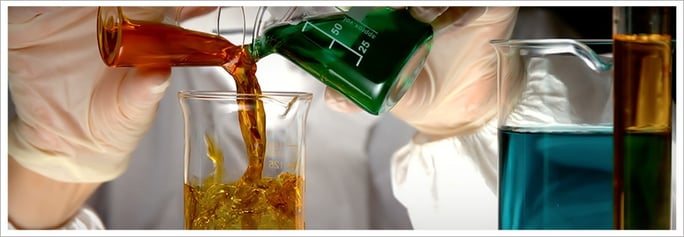
- What temperature range will it need to withstand?
- What does the chemical environment look like?
- What does the atmospheric environment look like?
- How much pressure will it be exposed to during daily use?
While one gasket material may perform extraordinarily well for a specific application, it could be entirely wrong for another. Some gaskets, made from Buna-N, are biodegradable and will break down or dry-out over time. Teflon enveloped gaskets may be great for a specific instance, but once the load is relieved the material will remain compressed and need to replaced. Dry, leaking, degrading, or failing gaskets all contribute to low life expectancies, increased maintenance, and the rising cost of preventative measures.
A Customized Gasket Solution
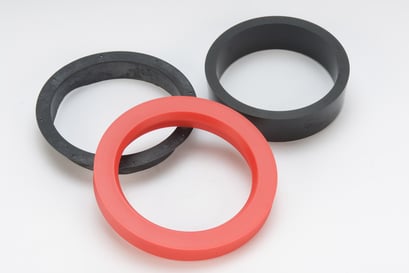
By turning to a custom composite provider, you can formulate a gasket to perfectly perform in your desired environment. As an example, perhaps you are looking for a material with a durometer lower than traditional rubber gaskets provide or maybe you need a series of gaskets color-coded to increase operational efficiency. All of these requirements - and more - can be solved with a custom composite solution.
Since 1997, Globe Composite has manufactured a variety of gaskets for the U.S. Navy, ranging as large as 139 inches in diameter, using a polyurethane based thermoset elastomer, Brandonite® 1200-60A. This flexible, high strength & highly elasticity material was created to combine the following properties:
- High tensile strength and outstanding elasticity
- Superior resistance to abrasion and tear
- Excellent energy absorption
- Low creep and compression set properties
- High resistance to seawater, oils, chemicals, and UV degradation
Due to its versatile and liquid-castable properties, our flexible, high strength, & highly elastic material can be used to produce one-piece gaskets or seals of almost any size or geometry that are knit-free and void-free. Our unique molding process can significantly lower tooling costs compared to traditional compression molded rubber products.
Brandonite® 1200-60A can be modified to increase (or decrease) certain physical properties such as tensile strength, rebound, durometer, or elongation to best fit your specific performance requirements. Defense applications aside, this mold-resistance, high-performance polymer naturally lends itself to submersible, agricultural, tropical, and water/sewage treatment applications. It is also available in FDA-approved grades.